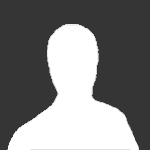
Unable to remove operating handle from bolt
Started by
j.rivet,
32 posts in this topic
Create an account or sign in to comment
You need to be a member in order to leave a comment