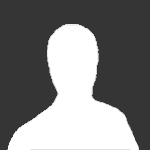
Joseph Scott
Members-
Content count
805 -
Joined
-
Last visited
Posts posted by Joseph Scott
-
-
I have new butt plates and original screws for $30 plus postage. Message me, will reply after thksg.
-
If the barrels have the original contour, they will weigh the same and have no effect on functioning. I have never seen or heard of a "heavy" barrel, or having a different contour (except the 7mm), remember gun is designed to function with bayonet attached.
-
The one marked "J. A." with four/five digit number is factory original. I believe the one marked "JS" is one I made using a CNC contoured Shilen blank. Of all the aftermarket barrels I have seen, none were marked by the maker except mine. I worked from original blueprints and did not mark a barrel until after I tested fired it. Most commonly, replacement barrels were made from M1 Garand barrels.
-
I will be downstairs with Johnson parts, three Johnson's and other military rifles to sell. Will be selling my 40 yr collection of Japanese 3- barrel flare guns and other rare Japanese items. Free Johnson inspections.
-
I have some bolt catches left that I have fitted to my guns. $125 plus $6 postage. Satisfaction or exchange/return. Message me.
-
Remove the front sight, turn front of barrel to diameter that just removes threads. Make a sleeve that is a slight press fit and length to half way between sight pins. Make it over size and slightly long, then turn it to diameter, when installed. When you install sight, the front pin will lock sleeve in place. This will hide the sleeve junction. Crown end and blue. Pins are 2/0 Morse taper. You will need to borrow or buy a tapered reamer.
-
To correct excess head space, the barrel must be machined. removed the rear collar, sight and lug. Machine the shoulder and rear of barrel back exactly .060" (one turn of collar). This puts the front sight back on top. You must also recut the extractor slot .060" deeper. Then you must make a spacer .060" thick and install it behind the center guide. Ream new pin location. Install rear collar, You can then ream chamber to correct depth head space. The entrance taper is 82deg, break the edge of chamber slightly. On occasion, I found it necessary to move collars 1/8" (.125"). Do not cut the front of rear collar, it doesn't work.
Before starting, cut some round shims the diameter of shell base. Try .002, 005,.010" with the go gage and find out how excessive is the head space. Ream slow with lots of lube and test often. I am not doing any work or accepting orders due to blindness.
-
That is a Remington 8 op handle. It fits but lets bolt rotate too much for proper lock-up of lugs.
-
I have new ones for $25 plus postage. Message me.
-
Use regular super glue in the crack. It will penetrate all way to bottom and will be stronger than the wood. Also the crack is unlikely to spread because the recoil is through the cross keys, not the bolt stop plate. You also pin the glued crack with 1/16" brass stock repair screw as used by our military. They are hard to find but work well.
-
Yes, many were glued on. Take a butcher knife and small hammer and carefully split it off.
-
I have found that the bolt catches were fitted to each gun during manufacture by varying the length of the little "finger" for proper operation. I believe that as the importer assembled guns after cleaning, some bolt catches fit and worked properly. If so, the gun was sold with a working catch, if the catch didn't work, it was left out and gun sold without a catch. Some years ago, I purchased quite a few of the discarded catches and found that the finger lengths varied from the drawing. Few of them were same dimension. By welding on the end of finger and bringing to correct length, they worked properly. The original fitting was required because the magazine internals have some axial movement. Bending the long portion of the catch works in some cases, but not always.
-
I would have to see and handle the rifle to convince myself. 'Buy the gun, not the story' is always good advice.
-
All original forearms had the cut-out and cross-pin. Because the little spring which retained the pin was not available, it was common to install a blind (short) pin and make new wood cover it to keep it in place. The cross pin holds the magazine in alignment and is important to proper functioning. I used to make the retainers but no longer can see to do them. That little retainer had no part number and probably was considered part of the forearm from some supplier. If you have a cut out, the retainer is likely broken leaving part still attached to the wood with a small twisted nail. Save the nail. If anyone can find a 3/16" pin, with a spring loaded ball in the side, it would work. A short 3/16" roll pin would work also.
-
Winfield made many sporter versions. It may be for one of those.
-
i can't tell from your pictures as they are too close. Originals all had the long rear end. if the one on right does not have it, it has been cut off. There are lots of pictures on the web showing them installed.
-
That is a bolt stop plate which goes on the rear of a Johnson receiver. It slides down into grooves and the little plunger goes into a hole to retain it. The long end fits into the stock but is not a tight fit so it can remove for field stripping.
-
I offer $20 each for all of them. Joseph Scott
-
Walt, I have one set left but someone else has first pick, will know next week. May be 2-3 months for new wood blanks.
-
A new order classifying parts suppliers and gunsmiths as "manufacturers" requiring an expensive licence may affect supply of replacement parts or repairs. Google new executive order for information.
-
I am out of sights and bayonet lugs, both are in progress. However, it will be several months before they are ready.
-
To the best of my knowledge, the numbers were put on by other countries to reduce theft. I don't remember seeing a numbered bayonet until after Navy Arms imported some.
n
-
Looks like an unfinished home made job. The holes through the originals are to vent the air when cycling and the two rings are to reduce friction. The small cross hole on left side connects with a hole through from the bottom and these must be cleaned with small wire or drill. I have found many plugged with grease.
-
Yes, you can use same gages. In the gun, hook extractor over gage lip first and close gently. Operating handle should close on go gage (1.946") and not on no-go (1.950"). Do not force handle. If you do it out of gun, it is little tricky to get alignment. I have seen a replacement barrel which had a short chamber and would not close on 1.940" minimum gage. Every original barrel were within specs. A more common problem is superfine pitting in chamber making extraction difficult and preventing cycling.
in Johnson 1941 Rifle
Posted · Report post
There is no specific difference or location. The one with the "protrusion" is the latter version to aid in pulling them with rim of cartridges. I have new latter style pins for $15 ea. The early style finger could be broken off if the fit was tight and I suspect the latter version was to prevent this. Both the same is entirely proper.