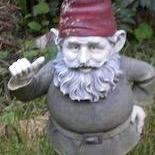
Removing the end cap for the recoil spring tube
Started by
eb in oregon,
22 posts in this topic
Create an account or sign in to comment
You need to be a member in order to leave a comment