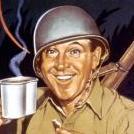
Another desporterization project
Started by
C P,
74 posts in this topic
Create an account or sign in to comment
You need to be a member in order to leave a comment
Started by
C P,
You need to be a member in order to leave a comment